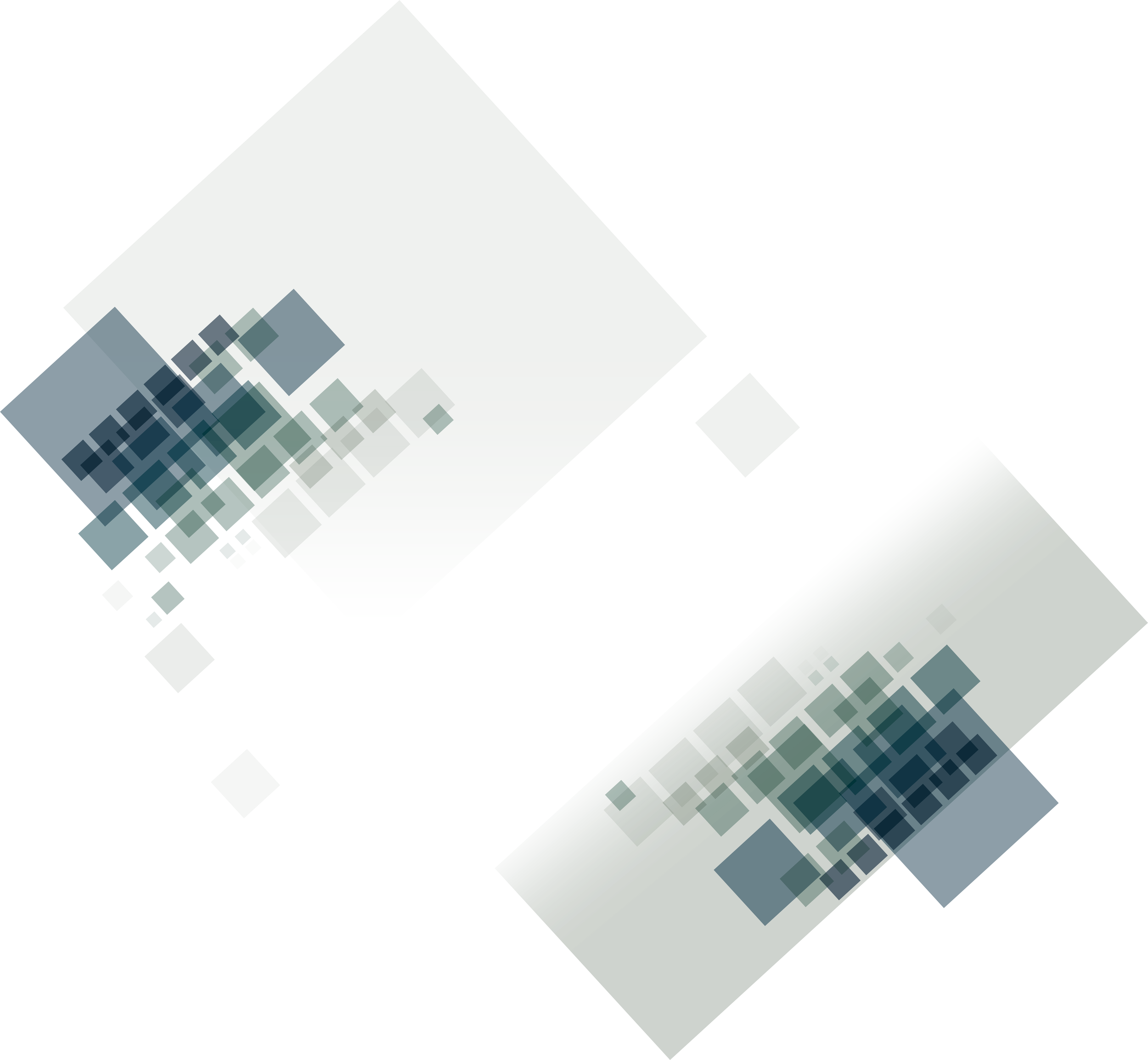
STRUCTURAL ALUMINUM
over 10 lbs
Xpeng inc., Alcoa Corp and Csmet
PART: XPENG G6 Front Cabin Mega Casting
MATERIAL: Alcoa EZCAST-plus C611N
WEIGHT: 119 lbs (54 kg)
END MARKET: Automotive
Caster Award Nominees: Luo WenZhi (XPENG), Xinyan Yan (Alcoa), Zhang YueBo (CSMET)
Customer: xpeng inc.
-
FUNCTION OF PART
The front cabin megacasting combines safety, weight savings, and structural integrity, making it a key feature in this electric SUV.
-
PREVIOUS PROCESS TO PRODUCE PART
Traditional assembly methods were used to join more than 50 high strength steel stamping components by welding and riveting. The single-piece megacasting not only simplifies assembly, but also enhances the structural integrity and reduces the weight of the vehicles.
-
ADVANTAGES GAINED
1. Alcoa EZCAST-plus C611N alloy was used in this application. The alloy can achieve more than 10% elongation and >120MPa yield strength in as-casting condition. The alloy eliminates the dedicated heat treat, and thus prevents the distortion of the megacasting (significant cost saving).
2. The front cabin casting helps protect occupants and the battery in case of a crash by directing impacting forces away from the cabin and battery.
3. The front and rear mega castings and CIB battery integration technology produce body rigidity up to 41600N-m, 83% greater than traditional designs.
4. The front cabin megacasting allows XPENG to replace >50 separate components with a single cast piece. This not only eliminates complexity, but also lightens the vehicle by approximately 33 lbs (15 kg).
The efficiency in the production process directly translates into a lighter, more structurally sound vehicle.